The drying of porcelain is one of the points where one must be particularly vigilant. Once throwned or removed from the mold, raw porcelain must be protected by plastic films.
If it is throwned, we let it dry in the open air because it is very wet. Once firmed, it must be protected by plastic films just laid.
If it is molded, the fineness of the piece will induce a very fast drying that must be stoped by completely covering with plastic.
Once it is leather hard, the pieces are ready for decoration or to put a handle. Then they go again under plastic just laid a few days and upside down.
Finally, when the clay really starts to dry, you can finish the drying in the open air.
In fact, in the manufacture of a piece, drying will take 3/4 of the time. So when I am ordered a piece, it is on average between 3 weeks and a month of delays!
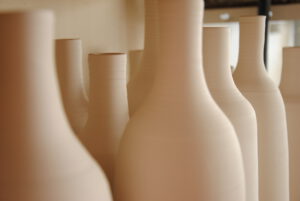